Reducing roughness correctly
Press release - 13.04.2021
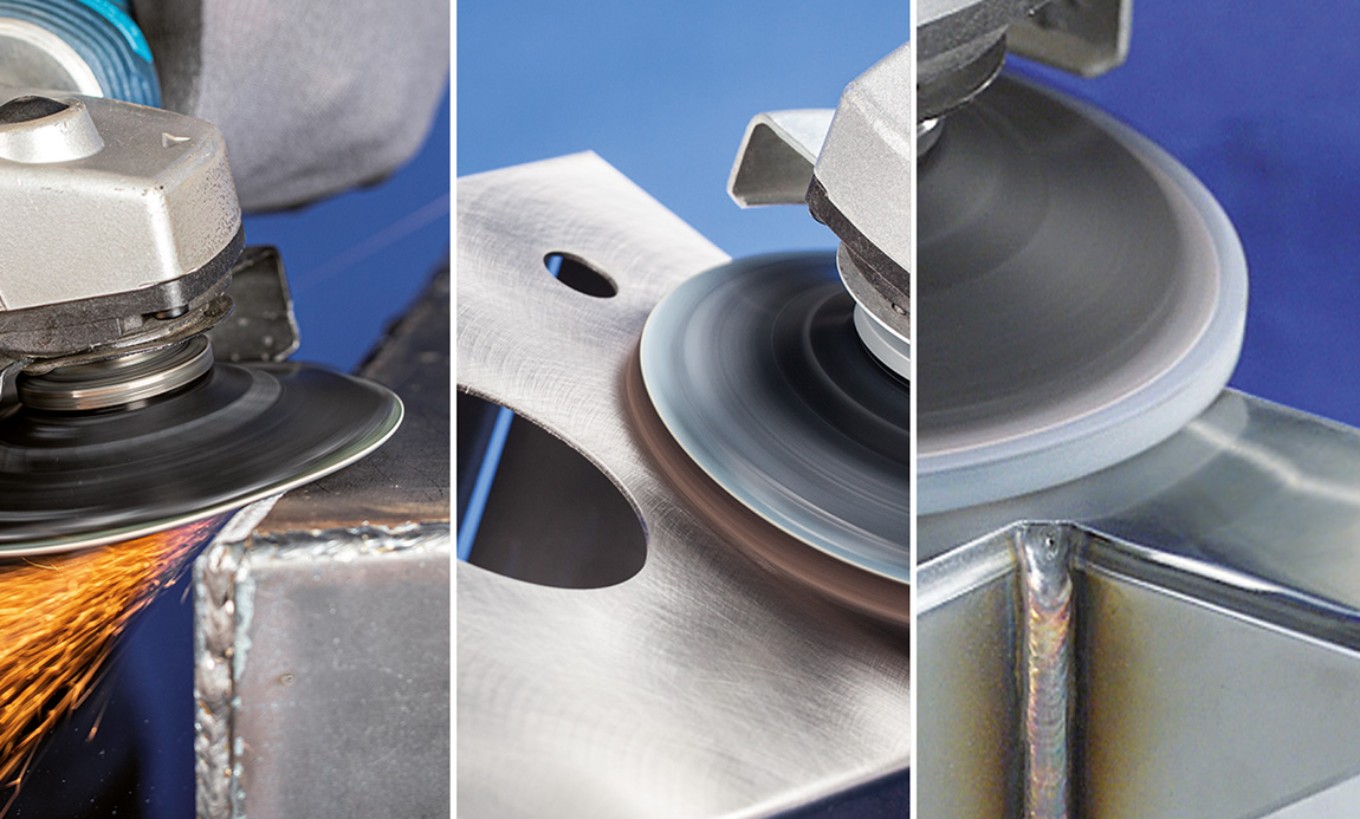
Even though it’s only every about obtaining the right roughness, working on surfaces is only effective if all the factors are balanced correctly. That’s the view of Ralf Heimann, a specialist in fine grinding and polishing.
“If we’re talking about surfaces, essentially it’s always about getting the right roughness”, says Ralf Heimann, product manager for fine grinding and polishing tools at the Marienheide-based tool manufacturer PFERD. “Because that what defines surfaces.”
But in practice what seems so clear and simple often turns out to be an extremely complicated application that regularly fails “if you don’t know what the influencing factors are”, says Heimann.
Surfaces and their functions
The first question to answer is what a surface actually is. “Technically speaking, surfaces are defined by their properties, for example roughness. But we can also describe surfaces in terms of their function, for example protecting against mechanical damage caused by wear or friction, protecting against corrosion by performing a barrier function, but also a visual function like reflection, absorption or aesthetic design”, Heimann explains.
The planned use of the relevant component defines the requirements that then have to be produced. And, as the product manager knows, that is often where there is a lot of uncertainty.
“Production of functional surfaces involves a lot of influencing factors. To achieve the optimum result technically and economically, it’s vital to balance these factors effectively when it comes to choosing the method, tools and drives used.”
Conditions for the perfect surface
The general conditions are determined by the material to be worked on, the initial situation and the desired result. “The choice of tools for cleaning and smoothing a steel weld seam, for example, is totally different from that for brush matting of stainless steel”, says Heimann, discussing two typical applications. This is because the materials and the applications have very different requirements in terms of the tools used.
Likewise, the dimensions of the surface to be worked and its accessibility play an important role. “Small, tight locations require different tools from large, easy to reach surfaces”, Ralf Heimann explains.
Range with no gaps
Even when each individual factor that makes up the general conditions can be clearly described, the complexity of work on surfaces comes from the combination of all the variables. “The variety of materials alone demands a huge range of different abrasive grain types, as not every abrasive can be used on every material. Depending on the initial situation and the result to be achieved, the tools used generally start with rough working, then fine and very fine grinding and finally polishing.” A modern range of grinding tools has to cover the full breadth and depth of these requirements. And within the range the relevant solutions have to be coordinated precisely with one another, “as to systematically reduce the roughness to get the desired surface finish, I need tools that are precisely designed for the individual steps”, says the man from PFERD. That is why the PFERD range of grinding, fine and very fine grinding and polishing tools is based on the needs of those carrying out the work and the results they are aiming to achieve. “There cannot be any gaps.”
Likewise, the shapes and designs of the tools have to be sufficiently varied for them to be suitable for any application. It is common for users to be faced with a situation in which they have the right tool but cannot reach the location they need to work on, for example because the shank of the tool is too short or the cutting point faces backwards and cannot be reached with a face-down grinding tool. “In this case, we think about different usage scenarios”, Heimann told us. “We offer the same tool for use in face-down, belt, peripheral or hand grinding. And in lots of different dimensions. As a result, we can be sure that work can always be carried out, no matter where the surface to be worked is located and how I can reach it.”
From this perspective
from rough to mirror polished
and
from face-down to belt and peripheral grinding to manual applications
in different shapes and dimensions
we have a range that covers almost all possible applications for tools and work on surfaces, according to Heimann. “And we know the best working strategy in each situation”.
Know-how
As part of its expert advice service, PFERD identifies solutions for the customer’s specific application situation. “We look at exactly what the customer is doing, where they want to go with their working and make suggestions for improvements.” Primarily, our aim is to ensure that the best possible result is achieved from a technical point of view. We pay particular attention to achieving the maximum possible efficiency and creating lean processes. Ergonomic working also places an important role and has effects in three areas: On the work result, on efficiency and, last but not least, on the person performing the work, who has to be looked after. “If we can literally get together with our customer at the workbench, we always achieve a significant improvement in the work result and the process”, Heimann reveals. The work invested here pays off very quickly.
“We have advised lots of users and found solutions for their problems”, the PFERD product manager told us. “When we finally have the solution in front of us, customers are frequently surprised by how easily, quickly and effectively we managed to solve their problem. When it comes down to it, it’s always just about reducing roughness. But doing it properly.”